Case study of BFW solving critical challenges of a two wheeler manufacturer seeking customised solutions for the production of cylinder blocks for its two wheelers.
A two wheeler cylinder block is an integrated structure/component comprising the cylinder(s) of a reciprocating engine and often some or all of their associated surrounding structures, such as, coolant passage, intake and exhaust passages and ports, and crankcase.
The cylinder block is the main structure within which the engine’s cylinders are housed. The primary function of the cylinder block is to support and align the pistons as they move up and down during the engine’s operation, facilitating the conversion of fuel into mechanical energy.
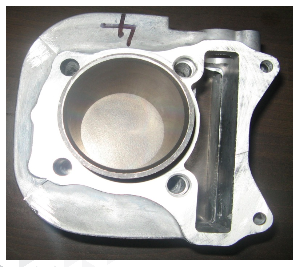
Our client
Our client is a reputed two wheeler manufacturing company, manufacturing and supplying a range of two wheeler vehicles across regions.
Highlights of the case
Our client required multiple Vertical Machining Centers (VMC) for manufacturing cylinder blocks. They had specific requirements, which included, 1.5 minutes per component cycle time, 4 variants of cylinder block (100cc to 250cc), and set up change time between variants of less than 10 minutes.
Our clients requirements and challenges
Our client sought multiple machining solutions to streamline cylinder block production on their shopfloor. Their key concerns were streamlining the production process of different variants of the cylinder block, ranging from 100cc to 250cc. To achieve this, they would require to change the set up for different variants; a scalable production solution that would meet the varying volume requirements without compromising the quality.. Their aim was to reduce set up change time to less than 10 minutes. Moreover, they wanted to aim for 1.5 minutes per component cycle time.
- 1.5 minutes per component cycle time
- 4 variants of cylinder block (100cc to 250cc)
- Set up change time between variants required less than 10 minutes
- Aluminium block with cast iron liner
BFW’s solutions helped achieve the client’s requirements
BFW’s expertise in precision engineering and customisable manufacturing solutions helped the client to overcome the challenges. Our teams collaborated with the client to understand, conceptualise and create a tailored machining line for the client. We provided three VMCs performing different functions per line, for four machining lines.
1. VMC 1: For bolt holes and dowels – crankcase side and head side
2. VMC 2: For milling, drilling, drill-tap – tensioner side
3. VMC 3: For cycle bore, rough and finish- head side
Here’s an illustration that explains the set up.
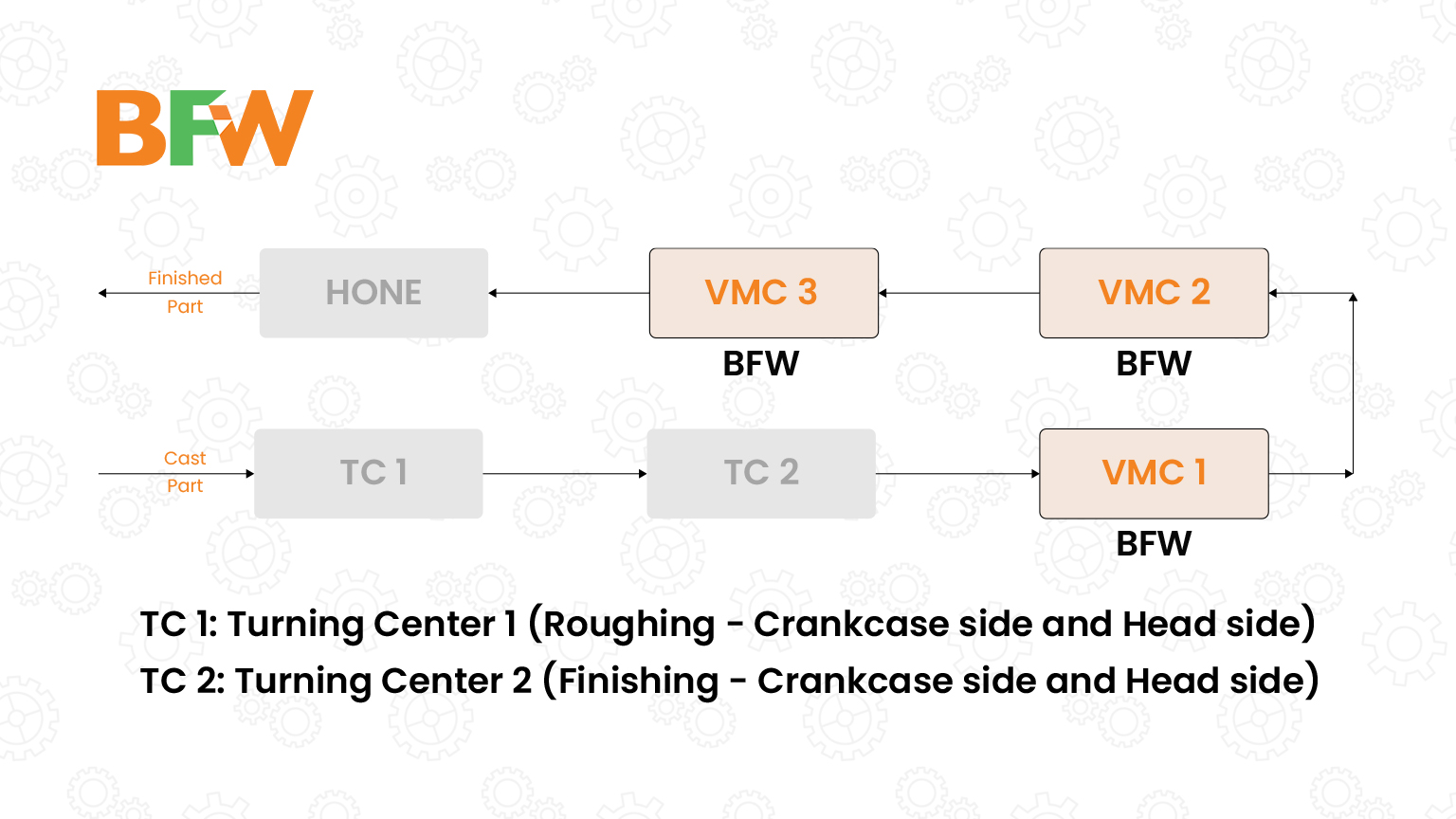
Other details:
- Takt time between the completion of one component and beginning of the next: 1.5 minutes
BFW VMC employed to address the client’s requirements: HSTC 4050 – Dhruva+
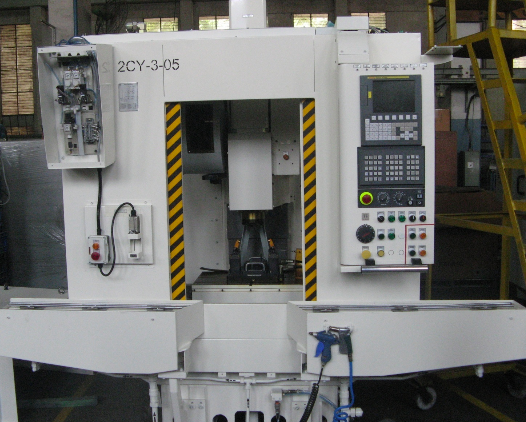
Features of HSTC 4050 – Dhruva+:
- Axes Strokes (X/Y/Z): 500/400/450 mm
- Table Size: 650 x 400 mm
- Rapid Traverse – 60 m/min
- Spindle Taper – BT40
- Spindle Type: Inline
- Power : 7.5/15 kW
- Torque: 47.7/95 Nm
- Spindle Speed (Max.): 8,000 rpm
- Chip to Chip time: 2.8 sec
- 24 tool magazine
Impact
BFW’s cylinder block machining solutions delivered impressive streamlining and optimisation to the client. By reducing cycle and takt time, our solutions have enhanced productivity and efficiency. Our solutions helped reduce cycle time and takt time, optimising the production process. Our client was impressed that we could provide the required and reliable results through tailored solutions, solidifying their satisfaction with our services. BFW’s machining solutions have helped the client achieve their targets and enhanced their position in the two wheeler manufacturing sector.
Four robust machine lines: BFW has delivered four comprehensive machining lines for cylinder blocks to our client. Today, all cylinder blocks produced and used in two wheelers manufactured by our client are made with BFW machines, showcasing the trust and reliability in our solutions.
Seamless installation: Apart from creating customised machines for the client, our support teams ensured a seamless installation process, followed by training and support as and when required that contributed to the seamless integration of our solutions into our client’s operations.
On-time delivery: BFW is known for on-time delivery of machines, whether the solutions are simple or complex. We managed smooth, on-time delivery for this customised machining line. The timely delivery helped minimise disruptions to our client’s operations.
Precision: Our client required four cylinder block variants with configurations ranging from 100cc to 250cc. We ensured the highest precision with unmatched process capability through our solutions.
Conclusion
BFW’s portfolio includes a range of machining solutions for manufacturing machine tools of various sizes and materials required across industries, including automotive, aerospace, among others. Our machining solutions ensure high-quality individual components that meet a wide range of requirements of our clients. When we don’t have a ready solution, we go the extra mile to create and deliver a customised solution.
Utilising BFW’s machine Dhruva HE 4050, our teams collaborated to develop robust solutions tailored to the client’s needs. This exemplifies the versatility and effectiveness of BFW’s machining solutions, demonstrating our commitment to delivering innovative and tailored solutions to our clients. This case underscores BFW’s dedication to innovation and customer satisfaction, reinforcing our position as a trusted partner in the manufacturing industry.