Valves are critical components in various industries, regulating the flow of fluids or gases within a system. Automation in valve assembly involves the integration of advanced technologies to perform tasks such as fitting components, attaching actuators, inspecting for quality, and ensuring proper alignment with precision and efficiency.
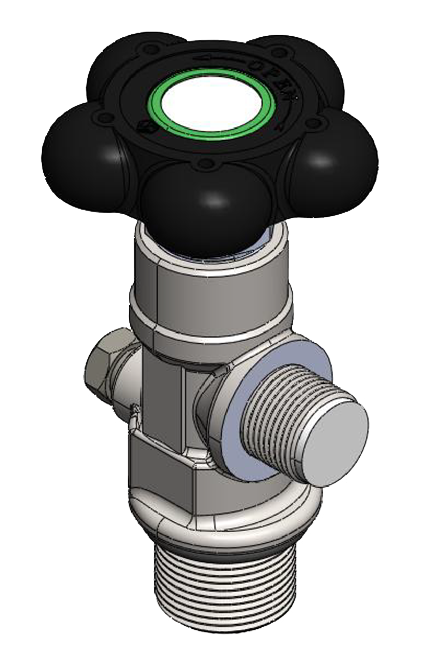
Automated systems streamline the assembly line, reducing manual labour, minimising errors, and increasing production speed. This approach enhances the consistency and reliability of the final valve products and contributes to cost-effectiveness and the optimisation of resources in the manufacturing industry.
The automation of valve assembly aligns with the broader trend in industrial automation, aiming to enhance productivity, reduce cycle times, and meet the rigorous standards required across various applications and sectors.
The client
The client is a reputed manufacturer of high-pressure gas valves. The company has been manufacturing gas valves for 50 years, serving global companies. The company proudly speaks of its products’ superior quality, performance, and safety. The company designs and manufactures cylinder valves for various applications requiring different operating mechanisms, devices, materials, and pressure ratings.
Highlights of the case
Automating the valve assembly system would bring several benefits to our client, from product accuracy to increased production to enhanced workforce safety, among others. Our client sought automation solutions to reduce the reliance on human resources and increase the overall product accuracy. Additionally, increased production and optimum utilisation of resources would lead to improved competitiveness in the market. Incorporating automation solutions would improve operational convenience and safety and guarantee stringent quality standards.
Challenges and requirements of our client
Our client’s existing valve assembly manufacturing process posed several challenges and sought to address the following issues:
- Reduce dependency on human labour
- Improve product accuracy
- Increase production
- Optimise utilisation of resources
- Enhance operational convenience
- Improve shop floor safety
The solution
BFW’s subsidiary company, m2nxt, designed, manufactured and supplied the assembly station for the value assembly as per the process details shared by the client. Our customised solution was designed to meet the client’s manufacturing process specifications. Our experts designed a solution to overcome the complexity involving multiple parts and components. In addition, we designed the automation solution with the safety of shop floor workers in mind and aimed to reduce dependency on human operators.
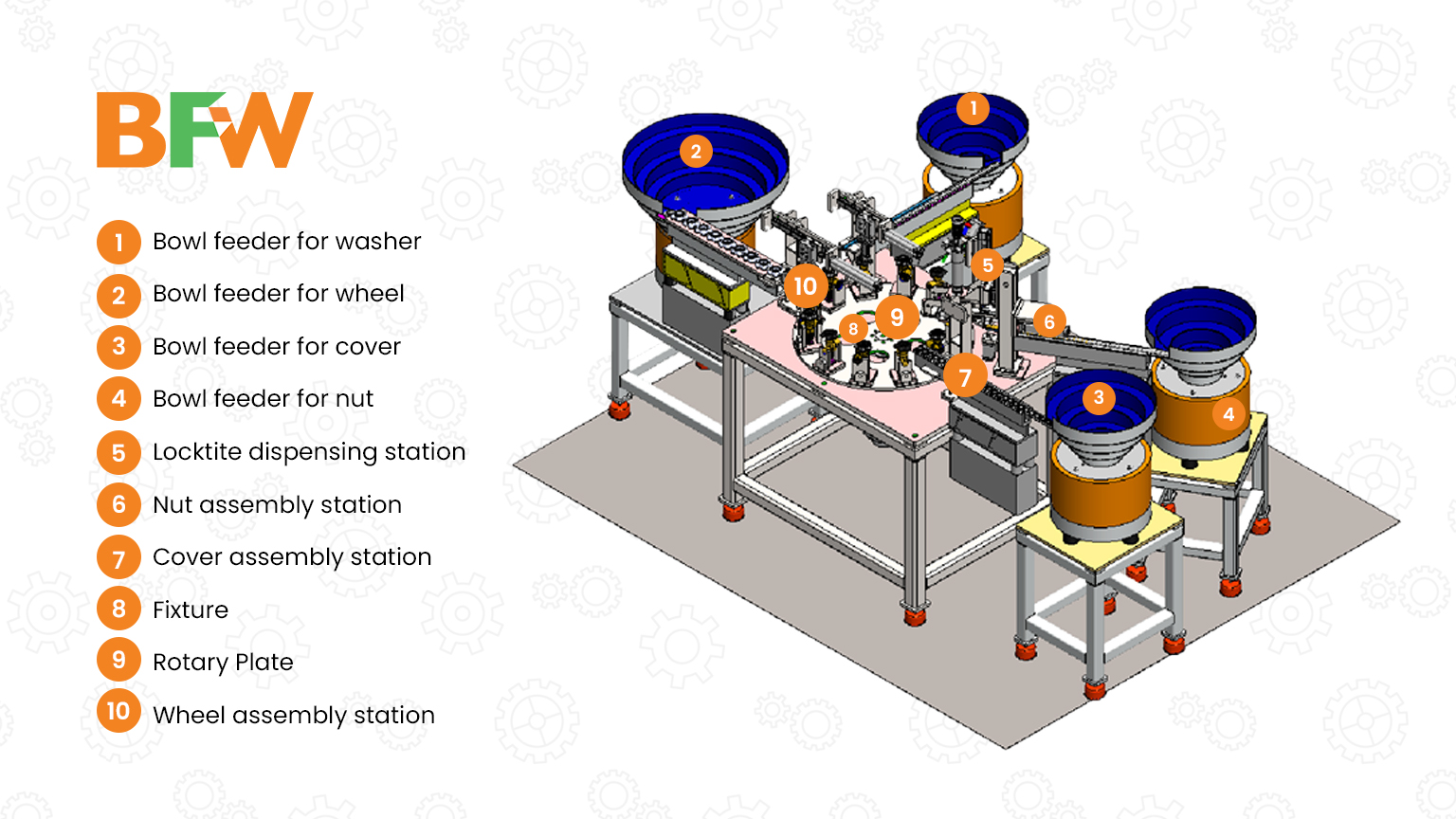
Impact
Our automation solution for the assembly station for the value assembly resulted in remarkable production optimisation for our client. An increase in productivity per shift of more than 300 parts resulted in a significant increase in the client’s annual output. With our automation system, the client was able to streamline operations, reduce human resources by one operator per shift, which in turn resulted in cost efficiency.
Here are some numbers:
- Maximum cycle time: 12.5 sec per component
- Productivity per hour – 288 nos.
- Productivity considering – 8-hour shift – 2304
- Productivity increase per shift: 304 parts
- Productivity increase per year (3 shifts/day, 300 days/year) – 2,73,600 parts
- Reduction of one operator per shift, hence three operators overall
Conclusion
In summary, integrating M2nxt’s automated assembly station for assembly valves represents a notable advancement in our client’s manufacturing operations. The manual process, which presented numerous challenges and limitations, has been significantly improved through the seamless operation of the automated system. This enhancement contributes to an overall streamlined manufacturing process for our client.
Collaborating with M2nxt brings additional advantages, including a lasting customer relationship, dedicated customer support, emergency assistance, post-installation services, training opportunities, and seamless possibilities for future upgrades to automated systems. Our collaborative partnership with our client has proven to be rewarding, yielding substantial benefits for our client’s operational efficiency and long-term success.