Today’s market is dynamic. Process plants must be competitive to survive. Complete visibility and control over every aspect of production and operations are essential for success. Embracing smart manufacturing is the key.
While there is awareness and acceptance for smart manufacturing, it is the implementation that may be a challenge to many manufacturing plants, especially to legacy production systems.
What is smart manufacturing?
Smart manufacturing is a method of harnessing the potential of Industry 4.0. It involves a network of machines capable of self-monitoring and overseeing ongoing processes, generating insightful data, and autonomously implementing actions.
The success of smart manufacturing depends on integrating various technologies into the process. This may involve using big data from Industrial Internet of Things (IIoT) devices and sensors, using analytics powered by Artificial Intelligence (AI) and Machine Learning (ML), adding automation and robotics, using Virtual Reality (VR) and Augmented Reality (AR) technology, adopting 3D printing, using cloud connectivity, taking advantage of 5G, using Computer Numerical Control (CNC) machining, and creating digital twins.
How does smart manufacturing benefit process plants?
- Smart manufacturing improves manufacturing plants on multiple fronts. By harnessing data, plants can optimise their processes. They can delve into real-time data analysis to gain insights across various aspects such as processes, resources, and assets.
- This heightened visibility enhances operational efficiency. It also contributes to increased safety for employees and the overall plant environment.
- Smart manufacturing drives innovation and accelerates time to market. By leveraging cutting-edge technologies and data-driven insights, plants can stay at the forefront of innovation. They can bring products to market faster. In addition, they can stay responsive to evolving consumer and market needs. Smart manufacturing is a transformative approach. It optimises current operations. It positions process plants for future success and growth.
- Smart manufacturing enables plants to pivot effectively during crises and respond adeptly to customer demands for customization and small production lots. The agility achieved through smart manufacturing is particularly notable.
- The implementation of smart manufacturing strategies allows plants to reduce waste significantly. This is achieved by minimising the number of poor-quality batches, transitioning physical tests to online simulations, and curbing energy waste. As a result, plants operate more sustainably and contribute to a more resource-efficient production process.
Implementing smart manufacturing in Manufacturing plants
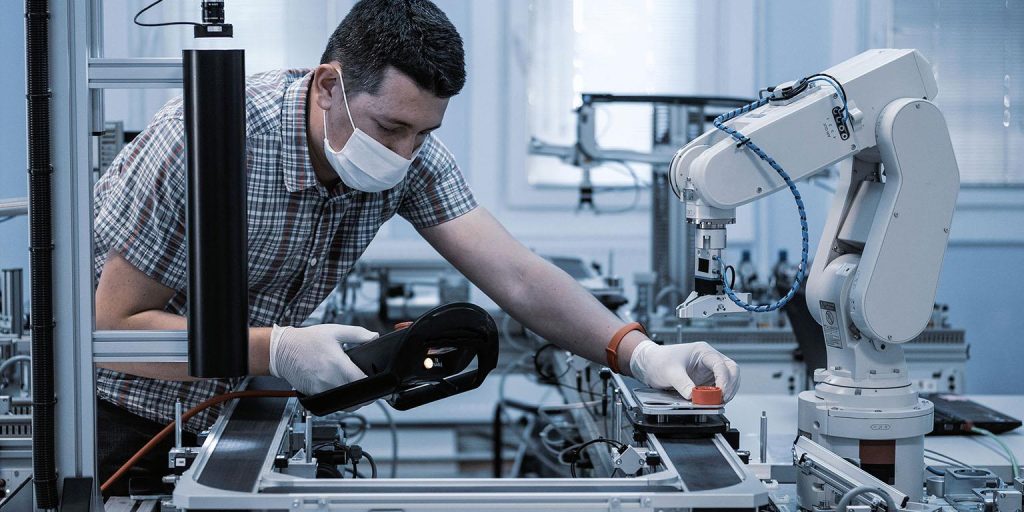
Implementing smart manufacturing in plants involves several key steps. The initial focus should be on advancing digitisation. Since smart manufacturing relies on integrated digitised processes, it’s crucial to transition manually run processes into digital formats.
An essential aspect is the improvement of data management. Big data serves as the foundation for smart manufacturing and AI/ML-powered processes. Therefore, it’s imperative to review data capture and storage protocols. It is essential to identify and eliminate bottlenecks and data silos. This ensures that algorithms have access to the necessary datasets for accurate predictions.
Cultivating a smart manufacturing culture is crucial. It aligns with the broader concept of digital transformation. Success in digital transformation depends on fostering a digital culture among employees. It is essential to ensure that staff understands the benefits and requirements of a smart factory. Training or adding new talent to acquire necessary skills is also essential. Management support from the top is another essential component.
Connecting networks and processes is another critical step. Many process plants implement digital projects and AI tools in isolated ways. They focus on specific areas of need and value generation. Smart manufacturing requires integrating individual assets and systems into a single, cohesive network.
Equally important is the attention to cybersecurity. Smart factories can benefit process plants in numerous ways. However, they also expand the attack surface and introduce potential security vulnerabilities. Continual testing of perimeter defences is crucial to safeguarding the plant against potential hacking attempts. Regularly checking the security profile is also essential. This proactive approach ensures the secure implementation of smart manufacturing practices. It also ensures their sustained operation.