Introduction
Case study of BFW solving critical challenges of a component manufacturer seeking a comprehensive solution for the production of pin shift finger machining solution.
A pin shift finger is a component or mechanism used in transmission systems, typically in automated or semi-automatic gearboxes. It is designed to engage or guide the movement of pins or gears to facilitate smooth shifting between different gear positions.
Pin shift fingers are integral to the precision and durability of the shifting process, ensuring proper alignment and minimal wear on related components. They are often engineered from high-strength materials to withstand repetitive motion and the stresses associated with automotive transmissions.
About our client
Our client is a notable company that manufactures critical, high-precision components for the automotive, windmill, and aviation sectors. The client was seeking a complete machining solution for the pin shift finger on a standard machining centre.
Challenges and requirements of our client
Our client faced some critical challenges in their existing production system. The challenges contributed to operational inefficiencies that affected production, customer satisfaction rates, and long-term sustainability. BFW addressed these problems with suitable solutions.
- Low productivity
Our client’s existing production process involved the use of multiple setups and different machines, causing inefficiencies in the workflow. The frequent downtime between transitions from machines slowed down the production rate. This resulted in longer lead times, reduced throughput, and an inability to meet the desired production volume within a given time frame.
- Difficulty achieving accuracies
Using different machines for different stages of the process often resulted in challenges with maintaining consistent quality and precision across the production run. For industries where high precision is essential (e.g., aerospace, automotive, medical devices), even slight inaccuracies can result in products failing to meet regulatory or customer standards or even causing failures in critical applications.
- Higher rejections
Due to the need for a standardized, streamlined process and the challenges in achieving accuracy, the customer experienced higher rejection rates of their products. Parts or components that did not meet the required specifications were often discarded or required reprocessing, further complicating the workflow.
Requirements:
- Higher productivity
- Greater accuracy
- Lower rejections
BFW’s Solution
We supplied one comprehensive Vertical Machining Center (VMC) for one component model – BFW Dhruva HE 4050. The solution includes the delivery of one machine with a single setup. The cycle time for this process is 4.95 minutes, with one model of the component in production. The material used for the pin shift finger is sintered steel.
Our expert engineering teams were able to achieve the exact accuracies that our client required. Here’s a table that illustrates our client’s accuracy requirement and the final accuracies achieved for the pin shift finger:
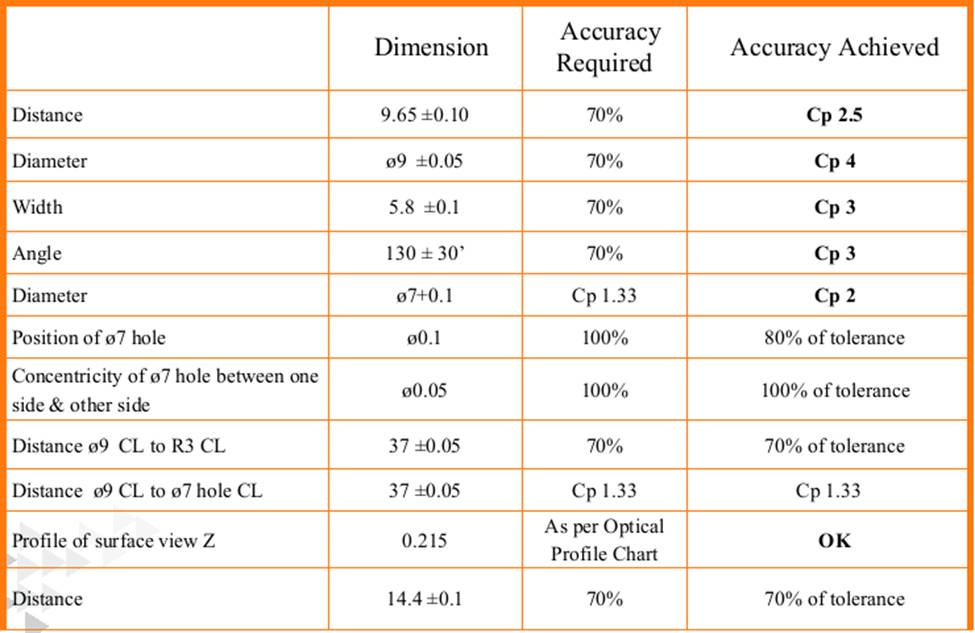
Machine features:
- Axes Strokes (X/Y/Z): 500/400/450 mm
- Table Size: 650 x 400 mm
- Rapid Traverse: 60/60/48 m/min
- Spindle Taper: BT40
- Spindle Type: Inline
- Power: 5.5 / 7.5 / 11 kW
- Torque: 35 / 47.7 / 70 Nm (cont. / 30 min. / 6 min.)
- Spindle Speed (Max.): 8,000 rpm
- Chip to Chip time: 3.2 sec
- 20 tool magazine
- Fanuc 0iMD CNC Control System
- 2 station rotary and tilting table
Here’s an illustration of the solution proposed by BFW for a comprehensive sequence for pin shift finger:
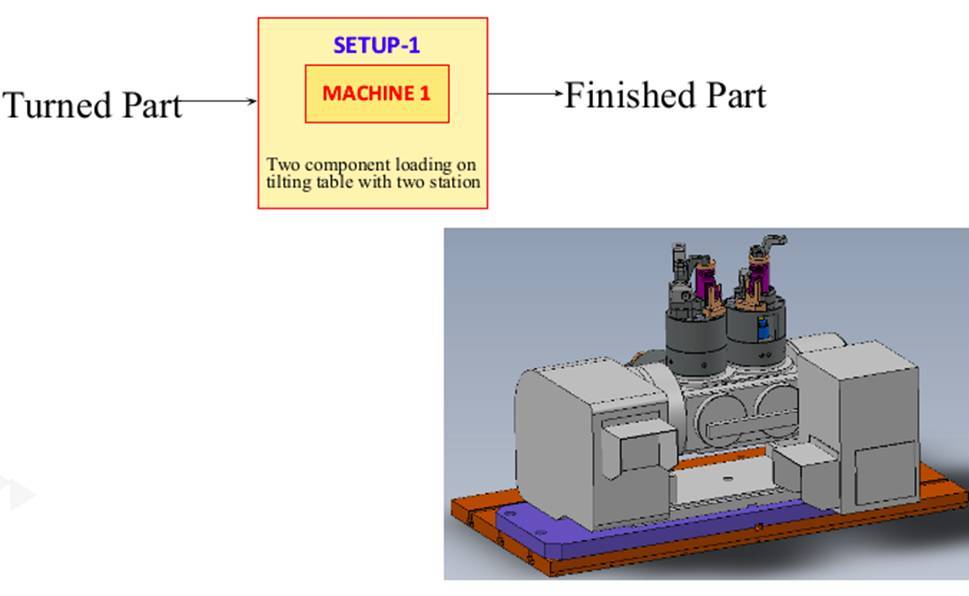
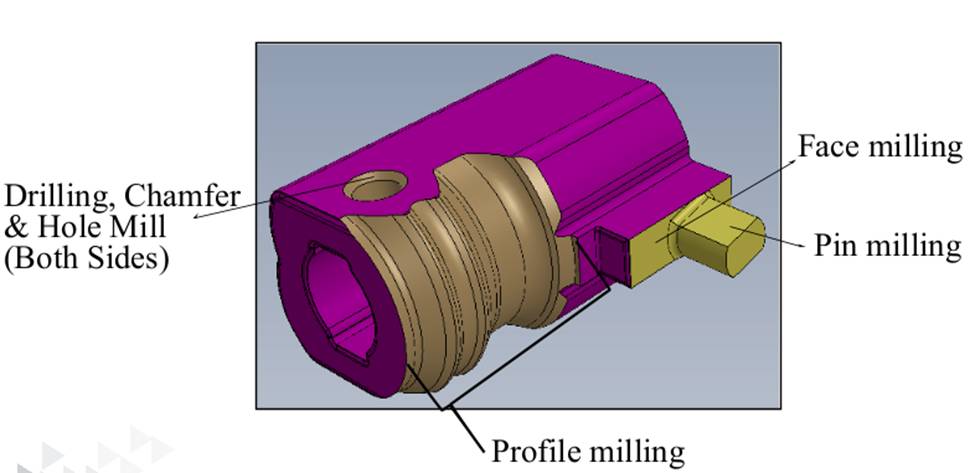
Project details:
- Machine: Vertical Machining Center (VMC)
- No. of machines supplied: 1
- No. of setups: 1
- Cycle time: 4.95 min
- Component model: Pin shift finger
- Component models: 1
- Component material: Sintered steel
Impact
BFW’s pin shift finger machining solutions significantly streamlined and optimized the client’s production process. By reducing cycle time, our solution enhanced operational efficiency. The client expressed high satisfaction with the reliable, tailored results we provided. As a result, BFW’s machining technology played a crucial role in helping the client achieve their production goals and strengthen their position in the manufacturing industry.
Conclusion
Through the use of BFW’s Dhruva HE 4050 machine, our teams worked closely with the client to develop customized solutions that addressed their specific needs. This collaboration highlights the versatility and effectiveness of BFW’s machining technology, showcasing our commitment to delivering innovative, client-focused solutions.