Energy efficiency is a critical factor in the machine tools and manufacturing sector. As industries continue to grow, the demand for energy has risen, making it imperative to optimise energy consumption in manufacturing processes. This article examines the value of energy efficiency in machine tools and manufacturing, the challenges faced, and innovative strategies to enhance sustainability.
Benefits of energy efficiency in machine tools and manufacturing
One of the primary motivations for prioritising energy efficiency in manufacturing is the environmental impact associated with excessive energy consumption. Conventional manufacturing processes often rely on outdated machinery that consumes substantial energy, contributing to greenhouse gas emissions and other environmental concerns. By adopting energy-efficient machine tools, industries can significantly lower their carbon footprint, aligning with global efforts to combat climate change.
Another compelling factor driving the emphasis on energy efficiency in manufacturing is cost reduction. Energy expenses constitute a substantial portion of operational costs for industries. Implementing energy-efficient technologies and practices not only helps in reducing utility bills but also enhances overall operational efficiency. This cost-effectiveness is particularly crucial in the fiercely competitive landscape of modern manufacturing.
However, achieving energy efficiency in machine tools and manufacturing is challenging.
Barriers to energy efficiency in machine tools and manufacturing
- One of the most prevalent challenges in the manufacturing industry is the lack of awareness regarding energy efficiency. Many manufacturers need to be informed of the possibilities and potential of new technologies and innovations that can facilitate the implementation of energy-efficiency strategies.
- Another challenge faced by manufacturing companies is the slow technological transformation or reliance on legacy manufacturing practices. Many manufacturing facilities still operate with outdated manufacturing systems and equipment that may not have the capacity for energy-efficient processes.
- High financial investment, or the cost factor, keeps manufacturing companies from energy-efficient tools, machines, and practices. Investments in energy-efficient machine tools and manufacturing systems often require substantial capital, posing a financial challenge for businesses, notably smaller enterprises.
- Another common barrier is resistance to change. In companies with ingrained established practices, employees may resist new energy-efficient technologies due to unfamiliarity, fear of job displacement, or concerns about disruptions to existing workflows.
Energy efficiency practices in the machine tools and manufacturing sector
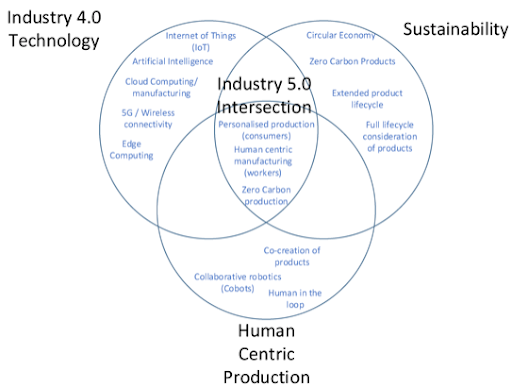
Circular economy
The concept of the circular economy has gained prominence in manufacturing, emphasising the importance of minimising waste and maximising resource utilisation. Adopting circular economy principles in machine tools design and manufacturing processes can lead to more sustainable practices, contributing to energy efficiency and environmental conservation.
Lean manufacturing
Assessing, monitoring, and optimising energy efficiency at the machine tools level is just one factor on the shop floor. Another aspect that also needs attention is the energy efficiency of manufacturing systems. Lean manufacturing offers many benefits to manufacturing systems that help with energy efficiency.
Smart monitoring and predictive maintenance
Machine tools equipped with smart monitoring systems and predictive maintenance capabilities can proactively identify potential issues before they occur. . Predictive maintenance reduces downtime and ensures that machines operate at their optimal efficiency levels. By averting unexpected breakdowns and minimising idle periods, manufacturers can optimise energy consumption and extend the lifespan of their equipment.
For instance, the integration of real-time monitoring systems enables manufacturers to gain insights into the energy consumption patterns of CNC machines during operation. This information enables adaptive control systems to adjust machining parameters to optimise energy efficiency. Predictive maintenance based on monitoring data further ensures that the CNC machine operates at peak efficiency, minimising unexpected downtime.
Energy-efficient drive systems
Integrating energy-efficient drive systems is a crucial aspect of enhancing the energy performance of machine tools. These systems provide for better control over speed and torque, adapting to the specific requirements of each machining task. As a result, energy is utilised more efficiently, reducing overall power consumption and operational costs.
For example, one of the primary avenues for improving energy efficiency in CNC machining lies in optimising toolpaths. Modern CNC software allows for intelligent toolpath planning that minimises unnecessary movements and reduces idle time. By streamlining the cutting process and minimising air cuts, manufacturers can significantly lower energy consumption without compromising the quality of the finished product.
Precision and control
Energy-efficient machine tools leverage advanced control systems and sensors to optimise machining. Precision in material removal and cutting operations ensures high-quality output and minimises wasted energy. By incorporating intelligent control mechanisms, manufacturers can achieve greater accuracy and reliability in their production processes, reducing the need for rework and the associated energy expenditures.
Adopting energy-efficient manufacturing practices
Convincing stakeholders to invest in these upgrades requires a comprehensive understanding of the long-term benefits, including reduced operational costs and improved competitiveness.
Moreover, there is a need for standardised benchmarks and guidelines to assess and compare the energy efficiency of different manufacturing processes and tools. Establishing industry-wide standards can facilitate informed decision-making and encourage manufacturers to adopt energy-efficient practices. Collaborative efforts between government bodies, industry associations, and research institutions are essential for developing and promoting these standards.
Innovative technologies are pivotal in enhancing energy efficiency in machine tools and manufacturing. Advanced control systems, sensor technologies, and predictive maintenance can optimise machine performance, reducing energy waste.
Moreover, integrating renewable energy sources, such as solar and wind power, into manufacturing processes can further mitigate environmental impacts.
Conclusion
In conclusion, energy efficiency in machine tools and manufacturing is a multifaceted challenge with far-reaching implications. The imperative to reduce environmental impact and the potential for significant cost savings underscores the importance of adopting energy-efficient practices. Overcoming challenges, such as upfront costs and the lack of standardised benchmarks, requires collaborative efforts from various stakeholders. Embracing innovative technologies and the principles of circular economy can pave the way for a more sustainable and efficient future in manufacturing.