Metal Additive Manufacturing (AM), often referred to as metal 3D printing, is a cutting-edge manufacturing technology that has revolutionized the way metal parts and components are produced. Unlike traditional subtractive manufacturing methods, where material is removed from a solid block to create a part, metal AM builds components layer by layer, offering unparalleled design flexibility and the ability to produce complex and customized parts.
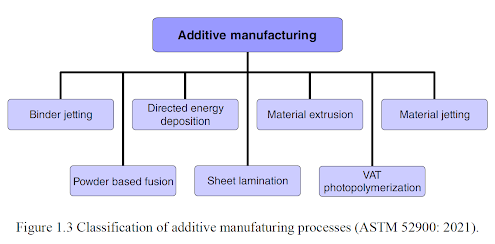
A detailed introduction to metal additive manufacturing
Metal additive manufacturing technologies:
There are several metal AM technologies, each with its own advantages and limitations. Some of the most common ones include:
- Selective Laser Melting (SLM): Uses a high-powered laser to melt and fuse metal powder in a controlled environment.
- Electron Beam Melting (EBM): Utilizes an electron beam to selectively melt metal powder layer by layer in a vacuum chamber.
- Direct Energy Deposition (DED): Deposits metal powder or wire material using a focused energy source, often through a nozzle, which allows for repairs, cladding, and large-scale part production.
- Binder Jetting: Sprays a binding agent onto metal powder layers, binding them together before sintering the part in a furnace.
- Powder Bed Fusion (PBF): Encompasses both SLM and EBM processes, where metal powder is selectively melted in a powder bed.
Each of the above Metal AM processes has its pros and cons. Some offer better resolution, some high build rates, some high build volumes, some offer multi-material capabilities, while some are capable of printing complex lattice structures.
However, the key challenges among these metal AM techniques, limiting their widespread industrial adoption are: part size limitations and slow build rates.
At m2nxt, we identified these key issues as significant barriers to the broader adoption of Additive Manufacturing. Therefore, we decided to strive forward to fill this gap.
To address these issues, Directed Energy Deposition (DED) is a process which is capable of both depositing at higher rates and also printing large parts. DED technologies are also expected to be the next game-changer in the Metal AM industry after the Powder Bed Fusion (PBF) process. Therefore, at m2nxt, we are looking at all the aspects of the DED process, including everything from the process to metallurgy, from lasers to electron beams, from wires to powders, and from parts as small as 50 mm to a parts measuring up to 5 meters in dimension.
We have envisioned a long- term plan to adopt the entire spectrum of technologies under the umbrella of DED. In addition, we are backed by the 60+ years of experience of our mother company, Bharat Fritz Werner Limited. This experience not only paves a path for us, but also gives us confidence to build DED machines of practically any size.
What is DED and Why is DED considered one of the most demanding techniques in metal additive manufacturing?
DED is one of the metal additive manufacturing processes used for creating metal parts. DED differs from other metal AM methods like selective laser melting (SLM) or electron beam melting (EBM) in several ways, making it unique and, in some cases, more demanding. Here’s an explanation of DED and why it can be considered one of the most demanding techniques in metal additive manufacturing.
DED is an additive manufacturing technique where metal material is deposited layer by layer to build up a part. In DED, material is usually added in the form of wire or powder. The key feature of DED is that it uses an energy source, typically a laser or electron beam, to melt the material as it is deposited, fusing it to the existing structure.
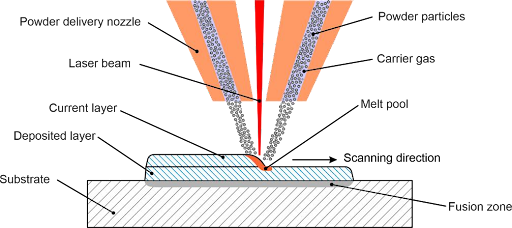
How does DED typically work?
- Material Deposition: Metal material, in the form of powder or wire, is fed into a focused energy source, such as a laser or electron beam.
- Melting and Deposition: The energy source melts the material as it’s deposited onto the build surface. The melted material fuses with the previous layers.
- Layer-by-Layer Building: The process repeats, layer by layer, until the entire part is created.
- Controlled Atmosphere: Depending on the setup, DED can be performed in an inert gas environment or even in a vacuum to control the atmosphere and prevent material oxidation.
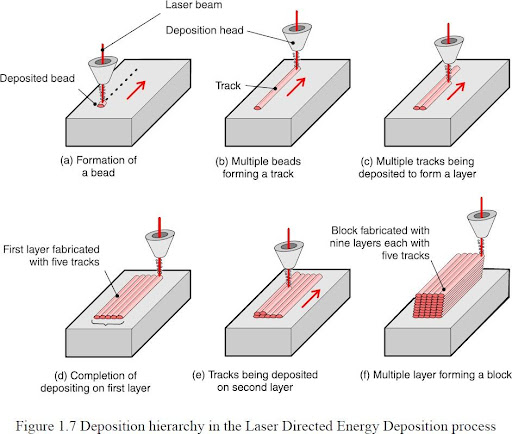
Why is DED a demanding metal additive manufacturing process?
Complex Process Control: DED involves precise control of multiple parameters, including energy source power, deposition rate, material feed rate, and nozzle or powder nozzle position. Achieving the right balance is challenging and requires expertise.
Quality Assurance: It is critical to ensure consistent material properties and quality throughout the part, including interlayer bonding. Variability can lead to defects.
Surface Finish: DED often produces rougher surface finishes compared to other AM processes. Extensive post-processing may be required to achieve the desired surface quality.
Overhangs and Supports: Designing for DED can be complex, especially when dealing with overhangs and unsupported features. Proper support structures are crucial.
Heat Management: The localized heat generated by the energy source can lead to thermal stresses, distortion, and warping. Managing heat and controlling part temperature are essential.
Material Selection: The choice of material, whether powder or wire, and the alloy used can impact process stability and part properties.
Large-Scale Manufacturing: DED is often used for large-scale parts, which brings challenges related to process scalability and maintaining quality over large build volumes.
Repair and Cladding: DED is also used for repairing or cladding existing components. Ensuring a proper bond between the added material and the substrate is critical.
Environment Control: Depending on the material and process, DED may require controlled atmospheres or even vacuum environments to prevent material contamination and oxidation.
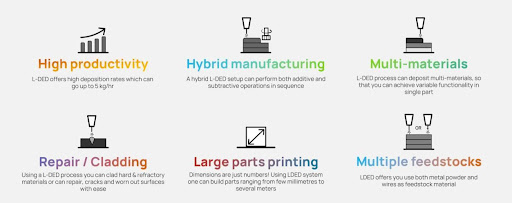
Applications of DED Process
1. Aerospace and Defence: The aerospace and defence sectors have been among the early adopters of DED technology. It offers benefits for repairing and refurbishing critical components in aircrafts, missiles, and military vehicles. Additionally, DED enables the production of lightweight and complex parts for aerospace applications.
2. Energy Sector: The energy industry, including oil and gas, has shown interest in DED for repairing and extending the life of equipment exposed to harsh environments. DED can be used to refurbish worn parts like pump components and valves.
3. Large-Scale Manufacturing: DED is well-suited for producing large-scale components and structures. Industries that require such parts, including construction, heavy machinery, and infrastructure, have shown interest in DED technology.
4. Repair and Maintenance: DED’s ability to repair worn or damaged parts without the need for complete replacement is particularly valuable in industries like transportation (railways, ships, and automotive), where downtime can be costly.
5. Customization and Prototyping: DED’s flexibility in terms of material choice and design freedom has made it attractive for prototyping and customized part production in various industries.
6. Research and Development: The development of new DED processes, materials, and equipment continues to drive demand, as researchers seek to improve the technology’s capabilities and expand its applications.
7. Additive Manufacturing Service Providers: Companies specializing in additive manufacturing services have also contributed to the demand for DED technology. These service providers offer DED capabilities to a wide range of industries, helping them meet their specific manufacturing needs.
8. Advancements in DED Systems: Ongoing advancements in DED systems, including improved process control, automation, and multi-material capabilities, have increased the attractiveness of DED technology for various applications.
Unlocking metal AM’s potential in industrial manufacturing with a holistic approach
So, what is the real potential of metal additive manufacturing for industrial ecosystems? And how can companies rethink manufacturing and business through the use of metal AM technologies?
Although giant manufacturers are already capturing notable benefits from metal AM technologies, many companies are still waiting for an effective framework that paves the way for positive returns on investment.
Addressing specific needs
The most common and routine application of metal additive manufacturing in industrial manufacturing is for prototyping to produce samples and unique components of large machines. Large companies and organizations are now exploring additive manufacturing solutions by identifying and analyzing pain points and restrictions in their current production processes. Metal additive manufacturing technologies are playing the role of enablers by addressing specific operational and business challenges of manufacturing ecosystems.
Collaboration, partnership, and networks
However, setting up in-house additive manufacturing systems requires huge capital investments. In addition, knowledge, competency, and talent. Therefore, today, most organizations take a collaborative and partnership approach. Companies are building networks with metal additive manufacturing service providers and manufacturers, such as m2nxt, to access technological capabilities, expertise, and capacity, thus gaining a competitive advantage in the market.
Mobilizing global ecosystems
Equally exciting is additive’s multi-stakeholder approach, bringing together academia, cross-border governments, and large corporations, among others into the network, thus, allowing greater resiliency and sustainability.
Conclusion – implementing metal additive manufacturing technology
Despite its demanding nature, DED is a valuable technology in metal additive manufacturing. It is particularly useful for applications like large-scale parts, repair work, and the rapid build-up of material for near-net shape production. With advancements in process control and material development, DED continues to find new applications and gain importance in industries such as aerospace, automotive, and oil and gas.
The manufacturing sector can gain more than just new business models and profits from additive’s potential and possibilities opening up in the near future.
But the implementation of metal additive manufacturing for industrial use requires more than a playbook. It requires companies to start with small and simple applications, and gradually increase the complexity levels.
And even to get started, presently, the best approach for companies and organizations is to collaborate and partner with larger companies that can lend their metal additive manufacturing technology competencies, knowledge, and capabilities.
m2nxt, a market leader in metal additive manufacturing technology, supports companies with the use of metal AM offering a comprehensive and evolving portfolio of capabilities, including its own ‘Made-in-India’ metal additive manufacturing systems.