A clutch cover is a casing or shield designed to encase and protect the components of a vehicle’s clutch system. This cover safeguards the clutch assembly, including the clutch disc, pressure plate, and release mechanism, from external contaminants such as dirt, debris, and moisture. By maintaining a clean and protected environment for these components, the clutch cover helps ensure the efficient operation and longevity of the clutch system.
About our client
Our client is a reputed automobile manufacturing company.
Highlights of the case
Our client, an automotive manufacturer, operated a clutch cover manufacturing setup that involved a two-face production process involving two different machines. This setup required transferring the components between the two machines for completion, resulting in significant inefficiencies. The need for manual handling and machine adjustments between production stages contributed to prolonged production times and heightened the risk of errors. Consequently, the overall productivity suffered. Moreover, the complexity of the production process made it challenging to streamline operations and ensure consistent output quality.
Challenges and requirements
Our client faced two main challenges:
1. Poor accuracy
2. Increased cycle time
Our client’s existing set up to manufacture clutch cover involved a two-face production process executed on separate machines. This setup required transferring components between the machines for completion, resulting in significant inaccuracies. The manual handling and machine adjustments necessary between production stages not only prolonged production times but also elevated the likelihood of errors. Consequently, overall productivity was low. Additionally, the complexity of the production process made it difficult to streamline operations and maintain consistent output quality.
Requirements:
- 82 seconds per component cycle time
- One component model
- Component material: aluminium
BFW’s solutions
We created a clutch cover manufacturing line for the client utilising Vertical Machining Center (VMC) Dhruva HE-3070. We created one customised set up including two machines to produce aluminium clutch covers.
In contrast to our client’s earlier set up that involved two machines, we reduced the number of machines to one. This reduced the complexity of transferring the component between machines, leading to a notable reduction in production time. Additionally, this also helped increase accuracy and reduce errors.
Dhruva HE 3070 features:
- Axes Strokes (X/Y/Z): 700/400/450 mm
- Rapid Traverse – 60/60/48 m/min
- Spindle Taper – BT 30
- Spindle Type: Inline
- Power: 3.7/ 5.5 kW
- Torque: 35 Nm
- Spindle Speed (Max.): 10,000 rpm
- Chip to Chip time: 3.2 sec
- 20 tool magazine
- Coolant through spindle @ 16 bar
- Hydraulic fixture
- Fanuc 0i MF CNC system
Representation of the operation sequence
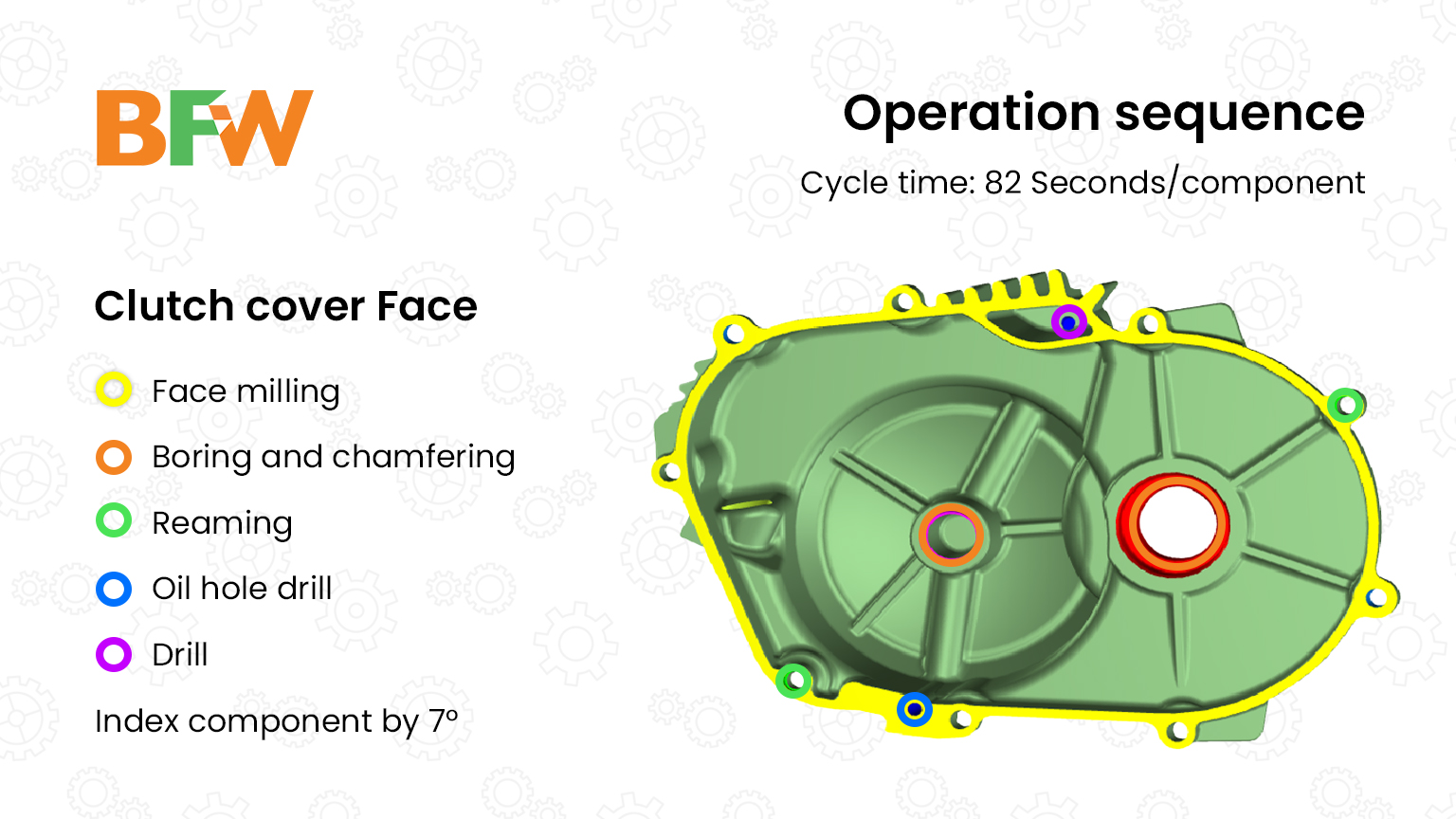
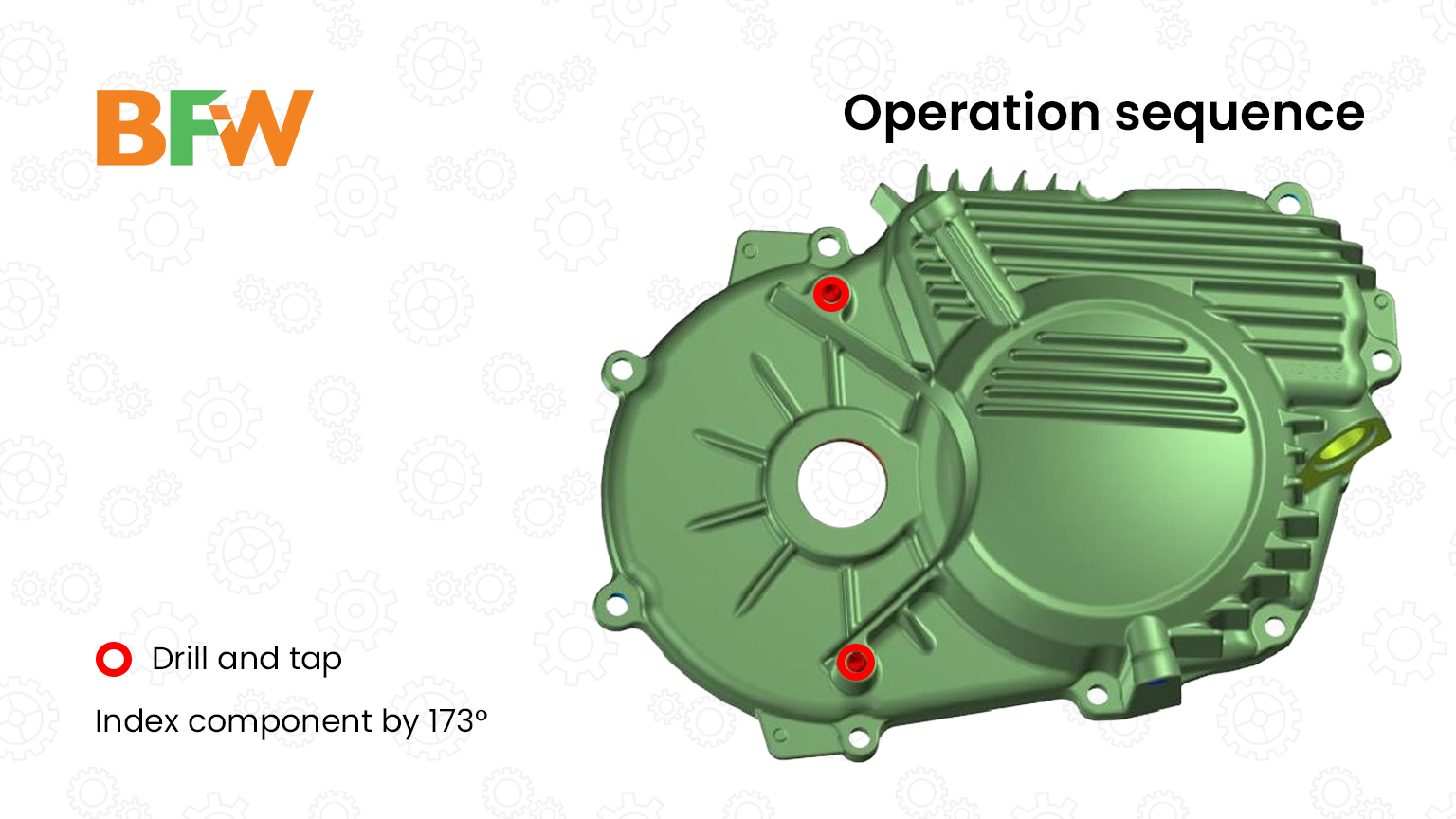
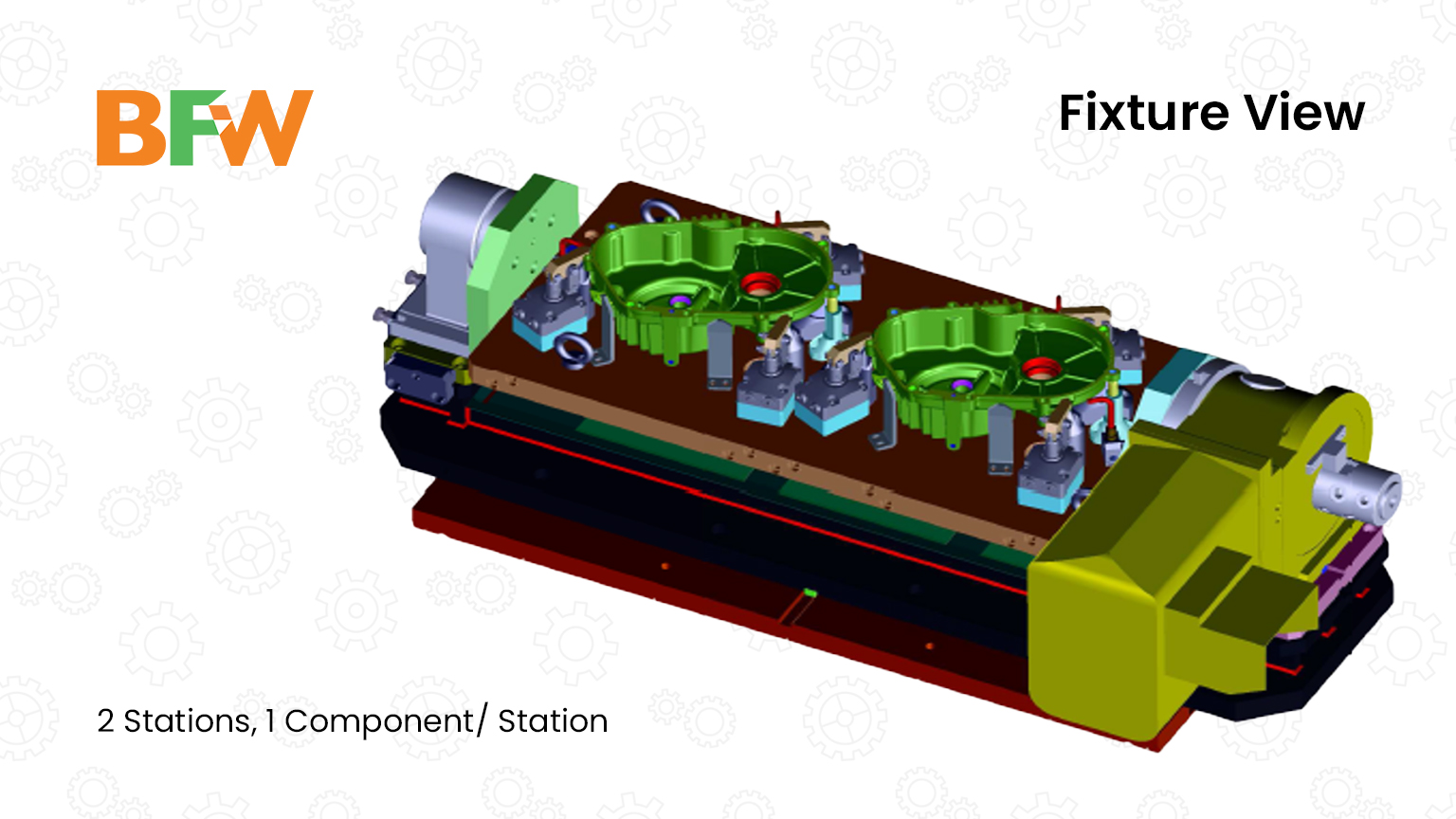
Impact
Our machine tool manufacturing solution resulted in remarkable production optimisation for our automotive manufacturing client. With BFW’s VMC solution – Dhruva HE 3070 – the client is now able to carry on the clutch cover production through one single machine, achieving a cycle time of 90 seconds, leading to substantial improvement in efficiency and productivity.
- Optimised production process
- Reduced complexity
- Improved productivity
Conclusion
Through BFW’s automated VMC for clutch cover production, we significantly optimised the client’s manufacturing operations. We were able to remove the challenges and limitations of the earlier process that involved two machines.
Engaging with BFW has brought additional advantages to our client. Our efficient customer support goes beyond delivery and installation. We ensure our client’s shopfloor teams are trained and given proper knowledge about the functioning of our machines. Our collaborative partnership with our client has proven to be rewarding, yielding substantial benefits for our client’s operational efficiency and long-term success.