Customised yoke machining solutions for reduced setup change time and 100% accuracy for an automotive manufacturing company.
Introduction
In automotive manufacturing, a yoke component is crucial. It ensures the efficient and coordinated operation of various mechanical systems. The term “yoke” generally refers to a device that connects or couples two or more parts. It allows them to move in tandem.
The design and material of the yoke are critical factors. They impact the overall durability and performance of the automotive system. Manufacturers meticulously engineer yoke components to meet stringent standards and accuracy. They do this to ensure reliability and safety in the final automotive product.
The client
Our client is a reputed, global market-leading auto component manufacturing company based in India. It is one of the largest companies in the auto component manufacturing sector, engaging in engineering, manufacturing, and distributing power-conveyance and energy-management solutions for vehicles.
Our client shares BFW’s beliefs and ambitions. They believe that the key to staying ahead of the competition is to use the latest technology and to do so, it is essential to partner with pioneering manufacturing companies to develop new capabilities.
Highlights of the case
In vehicles, more than one part can be called a yoke. Generally speaking, a yoke is a strap that holds a bearing in place. A yoke can hold a driveline, axle, or steering column. It can also hold a bearing in an engine, like a camshaft or crankshaft bearing.
The client realised that yoke machining in their factory took a lot of time to set up. This led to low productivity. The machining also did not provide the required accuracy resulting in a considerable number of rejections.
The client understood that it was essential to overcome these shortcomings for better efficiency, and the need was to look for a machine tool partner who would have or create an efficient, customised solution for them.
Designing and creating customised machine tool solutions is complex. Only a few machine tool manufacturing companies have the expertise, skill, capacity, and customised services to cater to such specific requests.
BFW has been providing customised machine tool solutions to customers across industries, including a range of highly specific solutions for the automotive industry. The client turned to BFW to help develop an efficient yoke machining solution.
Challenges
The key challenges for the client were:
- To reduce setup change time
- To achieve the required accuracy on standard machines
- To reduce rejections
- To increase productivity
Solutions
BFW’s expert design and engineering teams came together to provide the most efficient solutions. Step one was to identify the exact needs of the client. BFW’s team of experts identified three key features needed for the fixture:
1. Multiple component loading
2. Air seat check for component seating confirmation
3. Easy setup change facility
The next step was to create a detailed operation plan to create four tools. It involved the following:
- Design and creation of Tube, Flange and End yokes
- Use of forged steel to create the component
- BFW machine used: Horizontal Machining Center (HMC) PRIMA 44
Operation details of BFW’s solution:
Models:
1. Tube Yoke – 10042073
2. Tube Yoke – 10026551
3. Flange Yoke – 10047308
4. End Yoke – 10046362
Component material used: Forged Steel (SAE 1141)
No. of components loading/setup: 3
Total no. of setup: 1
Table size: 500 x 400
Average cycle time: 1.09 minutes
No. of tools: 4
BFW HMC PRIMA 44
PRIMA is a culmination of decades of experience in crafting Horizontal Machining Centers amalgamated with valuable customer feedback. Its diverse features cater to a wide range of manufacturing requirements. The PRIMA series of Horizontal Machining Centers has been designed to impact shop floor dynamics by increasing productivity, competitiveness and profitability. It has many innovative and first-in-class features, each contributing to enhanced reliability, performance and overall productivity.
PRIMA comes from the word “primary”, indicating a thing or person who has an overriding impact on everything around it. Some of its unique features, apart from standard and optional features, include:
- Pallet Size (500×400) mm
- Load Capacity: up to 400 kg
- Spindle speed maximum up to 8000 RPM
- T-type HMC
- Modular design
- Optimal structural design for thermal stability
- Designed to suit the adaptability of different kinds of applications
- High-quality spindle on precision bearings eliminates vibration under heavier cuts.
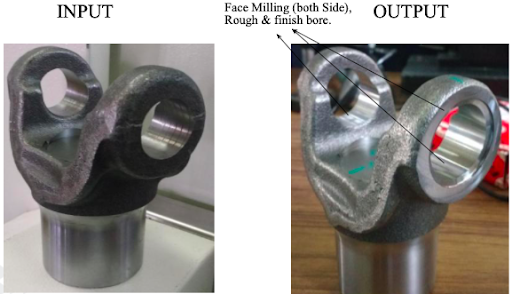
In the final step, BFW conducted a thorough inspection of the customised yoke components.
Key accuracies achieved by BFW’s solution:
Domension | Accuracy required | Accuracy achieved | |
Bore size | Ø 27 + 0.02/ 0.041 | Cp 1 | |
Span distance | 86.36 ± 0.2 | Cp 1.67 | |
Bore position | 0.1 | Cp 1 | |
Ovality | 0.007 mm |
Following the delivery, BFW engineers helped the client with installation and servicing needs. This ensured the smooth functioning of the new tools and their machines.
Impact
BFW’s customised solutions coupled with swift delivery helped the client quickly find a solution to their challenges. BFW-made yoke machining solutions helped the client enhance accuracy as well as minimise setup change time. This resulted in increased productivity, and reduced rejection rates. With our continued support and service, we helped the client align to their targets and ambitions in the automotive industry.