An external pin milling machine is used to manufacture machine tools designed for machining external cylindrical surfaces, pins and shafts, among others. This process is commonly used in the production of parts that require tight tolerances, surface finish, and the ability to machine complex external geometries. External pin milling machines are widely used in automotive( power transmission), Marine engineering and defence vehicles. Advanced technologies such as Computer Numerical Control (CNC), multi-axis machining, 4 or 5 axes, and high-speed spindles are used in external pin milling machines.
About our client
Our client is …..
Highlights of the case
Our client, in need of a machining solution for external pin milling fixtures, required a customised machine with unique configurations. These configurations were to ensure high precision, tight tolerances, surface finish, and concentricity. The client’s goal was to enhance their machining capabilities, increase efficiency, and maintain consistent product quality while meeting the industry’s high standards.
Challenges and requirements
Our client sought a customised external pin milling solution primarily to reduce cycle times and enhance production capacity. Their objective was to increase throughput by accelerating the external pin milling process while maintaining the highest standards of precision and quality.
They required a solution that could execute high-precision external pin milling operations faster without compromising accuracy, surface finish, or part integrity. Seamless integration with their existing production workflow was also critical, ensuring compatibility with current systems and minimising the need for extensive modifications or operator retraining.
The client stressed the importance of reliability and ease of maintenance. They required a machine that was designed for minimal downtime and consistent performance. The solution had to be robust, with straightforward maintenance procedures, to ensure long-term operational efficiency and maximise uptime in a demanding production environment.
BFW’s solution
We designed and created a CNC special-purpose external pin milling machining solution. Here are the details:
Component (input): Crankshaft
- Component: Crankshaft
- Component Material: Forged steel
- Hardness: ~270 ~325 BHN
- Max comp length: 700mm
- Min comp length: 300mm
- Max. comp swing: 220 mm
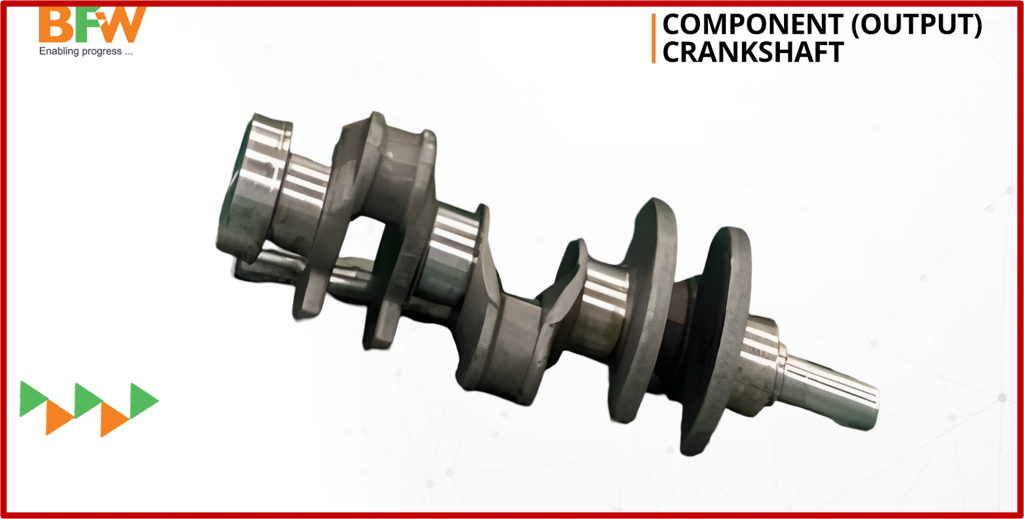
Component (output): Crankshaft
- Component Material: Forged steel
- Hardness: ~270 ~325 BHN
- Pin Dia – 38.85 mm
- Pin width – 20.75 mm
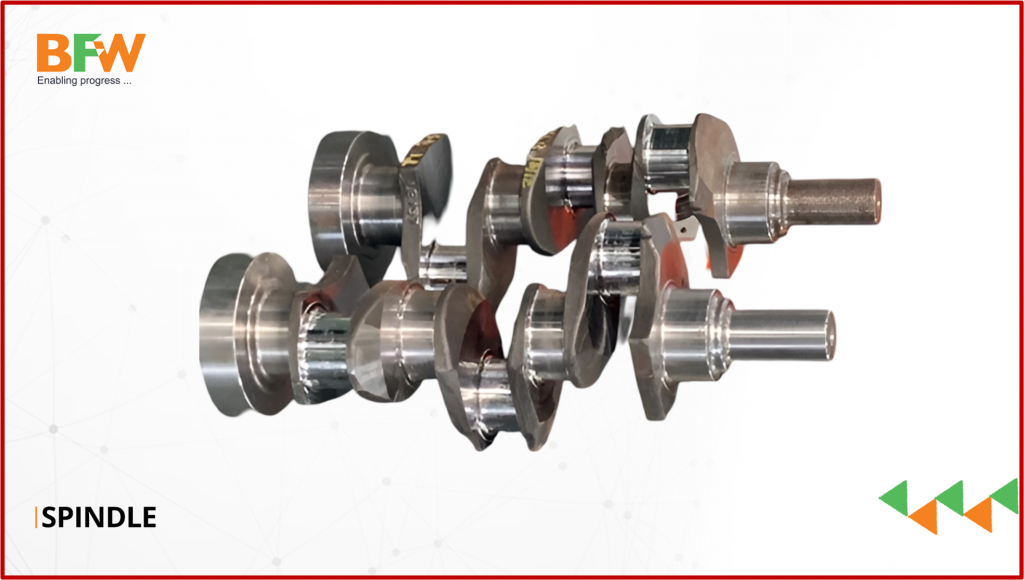
Spindle features
- Type of unit: Milling unit
- Spindle motor: 3ph, 400V, 37/45 Kw asynchronous motor
- Spindle speed: 40 – 150 rpm
- Spindle drive: Thru gearbox
- Spindle nose: Flange mounting
The fixture assembly overview
- Component loading and unloading: Manual
The fixture assembly was designed for manual loading and unloading of components. This manual operation allows for flexibility in handling different sizes and shapes of components. The system was engineered to ensure the operator can easily access the fixture, facilitating smooth and safe loading and unloading processes.
- Components per fixture: 1 no.
Each fixture is designed to hold a single component at a time. This configuration ensures that the fixture provides maximum stability and rigidity for the component, critical factors for precision external pin milling.
- Component location: Between two centres
The component is mounted securely between two centres, providing precise axial alignment. This method is ideal for external pin milling as it allows for accurate rotation of the workpiece along its axis, essential for maintaining concentricity and achieving uniformity across the milled surface.
- Component orientation: Keyway
The fixture assembly accounts for specific component orientation requirements, particularly in relation to a keyway. Proper keyway orientation is vital to ensure that all critical features align with the milling tool’s cutting path. The fixture includes precise indexing and alignment features that ensure the component’s keyway is correctly positioned, which is critical for achieving the desired machining outcomes in terms of accuracy and functionality.
- Component loading height: 1320 mm (from the ground)
The loading height of 1320 mm from the ground was ergonomically designed to ensure ease of access for operators during manual loading and unloading. The height is also compatible with standard material handling equipment, facilitating efficient transfer of components into and out of the work area.
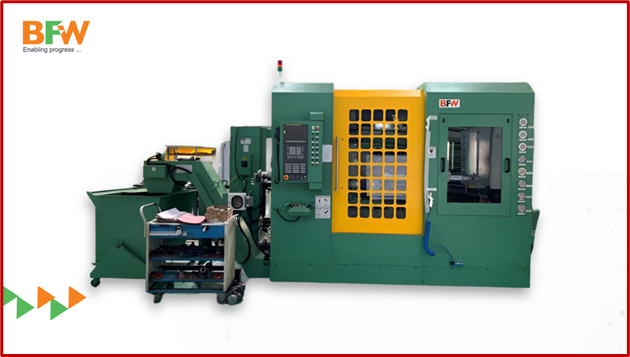
Impact
- Precision and repeatability: The between-centre configuration and precise component orientation ensure that every machined component meets exacting tolerances and specifications.
- Ergonomic efficiency: The carefully selected loading height reduces operator fatigue and improves productivity by providing an optimal working position for manual handling.
- Custom-fit: Tailored to the specific requirements of the component and keyway orientation, this fixture ensures seamless integration into the client’s production environment.
Conclusion
Leveraging our expertise in customised machine tool solutions, we optimised the client’s manufacturing process, addressing and eliminating their key challenges. The external pin milling solution, designed in close collaboration with the client, has significantly improved process flow, increasing precision and productivity across their operations.
By partnering with us, the client has gained additional advantages beyond the delivery of high-performance equipment. Our comprehensive customer support includes detailed training and continuous knowledge sharing, ensuring the client’s shopfloor teams fully understand and utilise the machine’s capabilities. This partnership approach has resulted in measurable improvements in the client’s operational efficiency and established a foundation for long-term success in their production environment.