Quality and Cost play a crucial role in the success of a machine tools manufacturing business. While quality and cost as standalone concepts are widely well understood, it is the optimisation of both that poses a challenge to many.
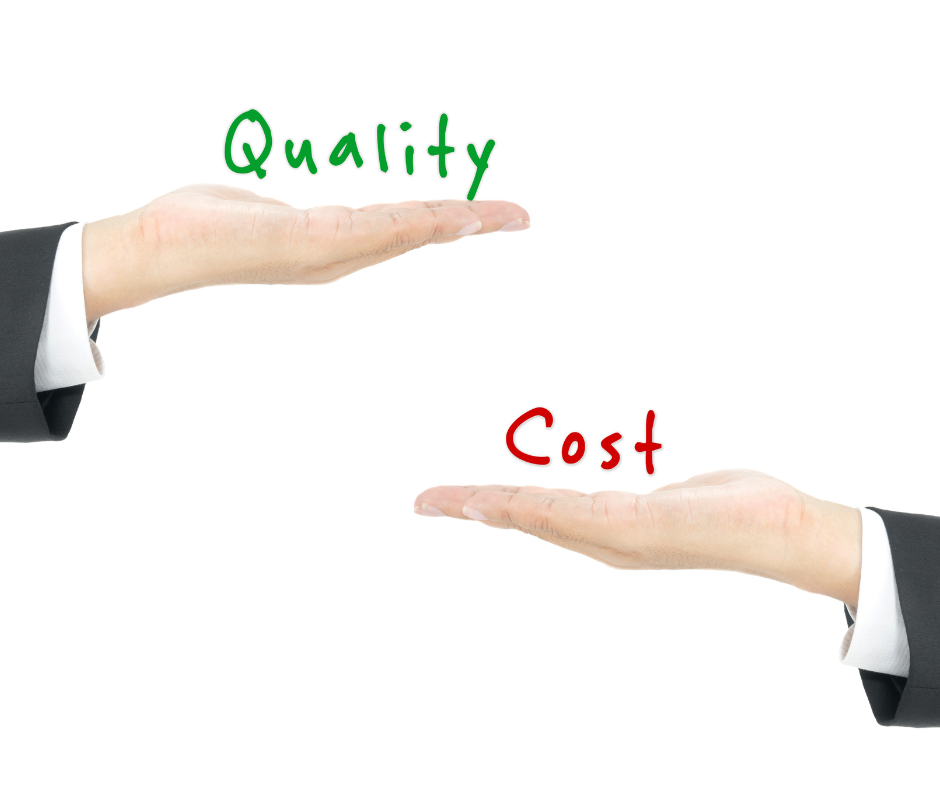
While quality is often associated with product excellence and customer satisfaction, cost is linked to the financial implication of producing and delivering the product. The cost factor goes beyond mere monetary considerations. It includes the careful allocation of resources, efficient utilization of materials, and waste reduction. In this delicate connection between Quality and Cost, manufacturers must navigate the path toward sustainable success, ensuring that the products meet high standards, and remain cost-effective for the customers.
Correlation between Quality, Cost and Asset tenure
Across industries, engineers and management teams erroneously attempt to simplify this optimization under the garb of the commonly used term ‘Value for Money’. While this is not grossly wrong, it underplays the possibility of striking a finer long-term value enhancement for the manufacturer (seller) and the customer (buyer). It is relatively easier and hence tempting to derive this balance at the ‘Initial Sale’ stage, but no organization can dissociate itself from the customer after the sale. Therefore, a more sustainable strategy must be built for longer engagement.
Here is where the concept of ‘Total Cost of Ownership’ and the ‘Life Cycle Costing’ technique become relevant, especially when the tenure of asset ownership is long. In fact, the longer the tenure, the stronger the case for using this approach for technical and commercial decision-making. A case in point is highly engineered products like transportation vehicles or capital goods.
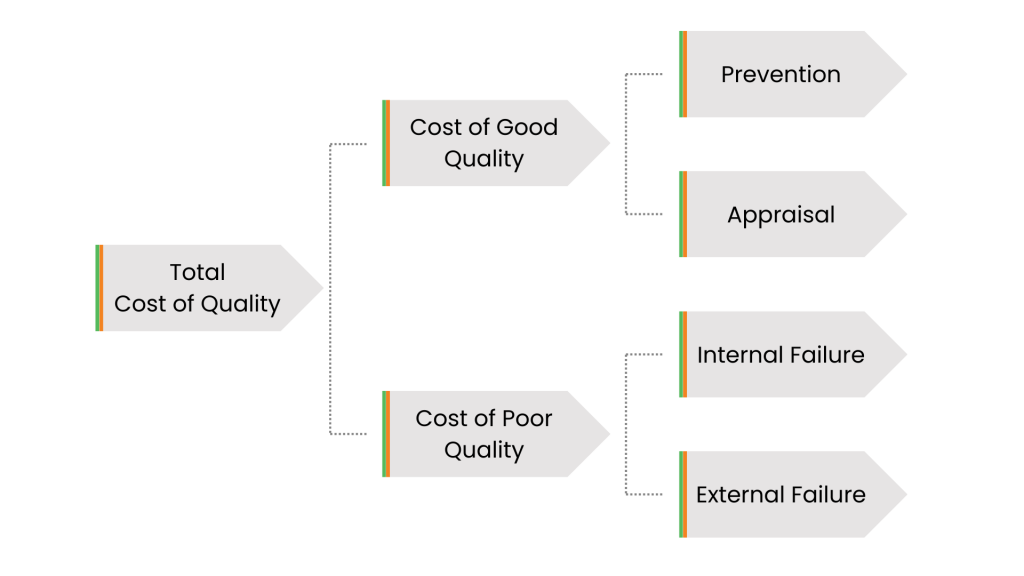
A strategic approach to balance Quality and Cost
Manufacturers must devise a strategic approach to achieve the right balance. It involves carefully evaluating both preventive and appraisal costs, considering minimising the potential impact of internal and external failure costs. Two perspectives must acquire dominance in this context –
- The running cost of the product includes operating costs, maintenance costs, warranty costs, rates of deterioration, reliability, etc.
- The hidden costs include the costs associated with lower quality assurance, component non-conformances, cost of procurement, delivery fluctuations, inefficient use of resources, additional design and development costs, etc. which some organizations try to classify as the broader CoPQ.
Further, a few progressive organizations have started considering environmental and social costs (e.g., cost of disposals at the end of the life cycle, circular economy options, etc.)
Since both of these aspects generally require an in-depth analysis, they force organizations to look beyond the obvious. However, the decision and the product offering emerging out of this approach are, more often than not, significantly better and hold the potential to achieve a much higher long-term ”QUALCOST“ value proposition for all stakeholders. Further, organizations can look forward to tremendous benefits if they get employees to innovate around this concept.