Introduction
The term “case transaxle” refers to an integral component within an automotive transaxle system that combines the functions of a transmission and axle into a single unit. The case transaxle houses various gears, shafts, and other essential components that facilitate power transmission from the engine to the wheels in front-wheel-drive and some rear-wheel-drive vehicles. This unit is responsible for not only transmitting power but also for distributing it between the drive wheels.
The design of the case transaxle is critical to achieving an optimal balance between weight distribution, efficiency, and space utilisation within the vehicle. This component undergoes precise engineering to ensure seamless integration with the overall drivetrain system, contributing to the vehicle’s performance, handling, and fuel efficiency.
The client
The client is one of the largest Japan-based automobile manufacturers in the world, producing millions of vehicles annually.
Highlights of the case
The client is a Japanese automobile manufacturing company, one of the largest in the world. The client sought to acquire seven machines with specific machining parameters and salient features. BFW designed and built customised machining solutions.
Client requirements and challenges
To enhance cycle time and accuracy, the client sought to acquire several high-precision Case Transaxle machining solutions for its manufacturing shop floor.
In automotive engineering, the imperative for precision and accuracy is particularly paramount when it comes to the design and functionality of a transaxle. A transaxle is a critical component in a vehicle’s drivetrain, combining the functions of a transmission and axle into a single integrated unit. The need for accuracy in transaxle design arises from its pivotal role in ensuring seamless power transmission from the engine to the wheels.
Precise engineering is essential to optimise gear ratios, torque distribution, and overall performance. Achieving accuracy in the design and manufacturing of the transaxle case is crucial to minimise friction, heat, and wear, thereby enhancing the efficiency and longevity of the entire drivetrain system.
Additionally, precise tolerances contribute to smoother gear shifting, improved fuel efficiency, and enhanced vehicle manoeuvrability, and improving cycle time. In essence, the demand for accuracy in case transaxle design reflects the industry’s commitment to delivering reliable, high-performance vehicles that meet the stringent demands of today’s discerning drivers.
Solutions
BFW designed and built customised case transaxle machining solutions for ADT 4 and aluminium fixtures. The overall dimensions of the case transaxle were 480mm x 130mm x 380mm.
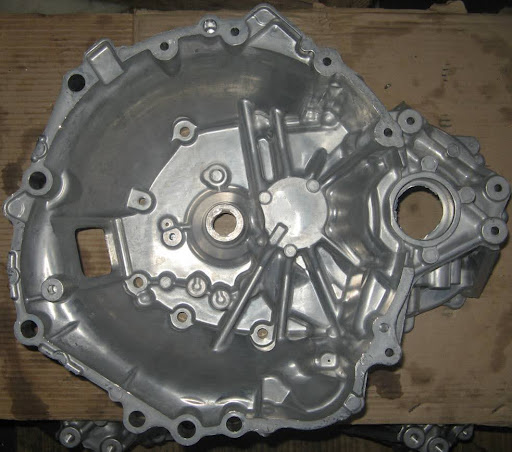
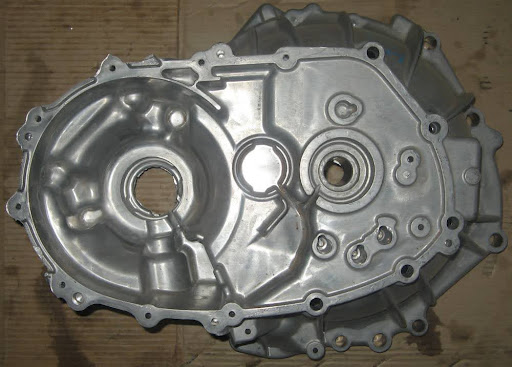
Particulars:
2 cells: 4 machines (cell 1) and 3 machines (cell 2)
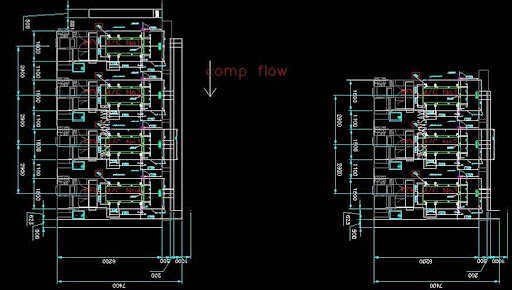
Takt time – 110 sec (cell 1) and 135 sec (cell 2)
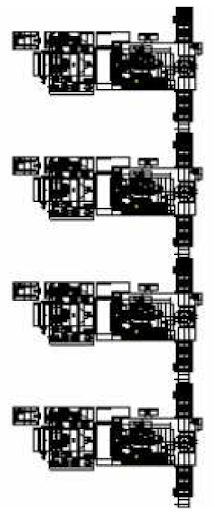
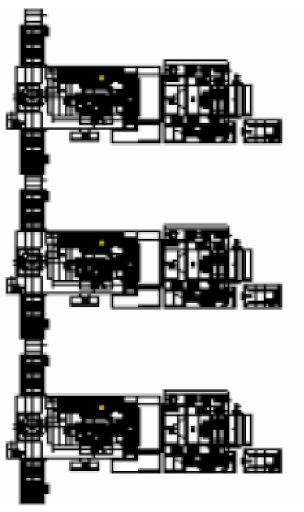
- Application Engineering
Our application engineers closely collaborated with the client’s team to understand their specific requirements and tailor the machining solution accordingly, ensuring the finer details of the requirements were met.
- Custom Workholding and Tooling Design
BFW designed the workholding and tooling to suit the critical accuracy requirements of the component; moreover, ensuring the customer’s ease of procuring the tooling, in the long run strengthens our partnership with the client.
- HMC 400MC VEGA
Backed by a team of seasoned industry experts, BFW offers a vast array of Vega H 400MC CNC Horizontal Machining Centers. These machines are aesthetically designed and precision-engineered for their higher performance and durable work lives. Moreover, all these Vega H 400MC CNC Horizontal Machining Centers are rigidly tested on various quality parameters to deliver a flawless range at the client’s end.
BFW developed two sets of machines for the client with various functions, including milling, boring, and drilling.
Particulars
- Cell 1- 4 Machines (Complete machining)
- Cell 2 – 3 Machines (Complete machining)
Machine salient features:
- Axes Strokes (X/Y/Z): 510/510/510 mm
- Pallet Size: 400 x 400 mm
- Rapid Traverse – 50 m/min
- Spindle Taper – HSK A63
- 20 tool magazine
- Ball-screw cooling
S. Finishing machine salient features:
- Spindle Type: Inline
- Power : 7.5 / 11 kW
- Torque: 70 Nm
- Spindle Speed (Max.): 10,000 rpm
Finishing machine salient features:
- Spindle Type: Integral
- Power : 11 / 18.5 kW
- Torque: 60 Nm
- Spindle Speed (Max.): 15,000 rpm
- Linear Glass Scales
Impact
The collaboration with BFW has proven highly successful for the automotive manufacturer. Through the integration of BFW’s case transaxle machining solutions equipped with cutting-edge technology, the client achieved unparalleled accuracy and enhanced cycle time in the process of manufacturing aluminium components.
BFW’s expertise in custom part design and the development of specialised machines addressed the client’s challenges, enabling them to meet the stringent requirements of the automotive industry.
The performance of BFW machines outperformed that of the previous machines, setting new industry standards. As a result of this successful partnership, the client has gained a competitive edge in their market. The dedicated support provided by BFW’s on-site engineers ensured seamless operations, further solidifying BFW’s reputation as a reliable and innovative machining solutions partner in the automotive machinery sector.