The Computer Numerical Control (CNC) manufacturing process involves pre-programmed computer software led functions. CNC is used to manage and control various kinds of manufacturing processes, including those that involve grinders, CNC routers, lathes, and milling machines.
Alongside, some manufacturing processes utilize cutting-edge technologies such as robotics, to automate tasks, enhance efficiency and streamline production processes. Besides these, shop floors also use gantry equipment and systems that are pre-programmed and automated.
Since these machines are CNC controlled, manufacturers often have concerns regarding safety hazards. For instance, some of the common types of hazards faced in CNC machine shop floors are machine parts sliding, unstable machines, faulty parts, fire, and mechanical hazards causing collision or crash due to spindle failure. Hence, it is important to secure CNC machine environments.
Manufacturing companies looking to improve shop floor safety have a number of methods at their disposal that may be reactive, preventive, and predictive in nature.
- Reactive: In a reactive approach, actions or repairs are conducted after the accident or collision, resulting in substantial production losses and high repair expenses.
- Preventive: A preventive approach decreases the frequency of events but does not entirely eliminate them. This method results in moderate repair costs and production losses.
- Predictive: The predictive method, incorporating condition monitoring, can forecast events before their occurrence, often leading to very few actual incidents. This approach is associated with minimal repair costs and minimal production losses.
BFW and m2nxt: safety culture
Bharat Fritz Werner (BFW) and its subsidiary company, m2nxt, being companies that take an employee-first approach, believe in deeply embedding safety culture for their workers. Identifying and overcoming safety gaps was key to improving safety outcomes for manufacturing companies in a sustainable way.
As a solution, m2nxt developed an advanced, predictive system to detect accidents before their occurrence and retrieve defects before damages.
Meet iVi, a collision detection system.
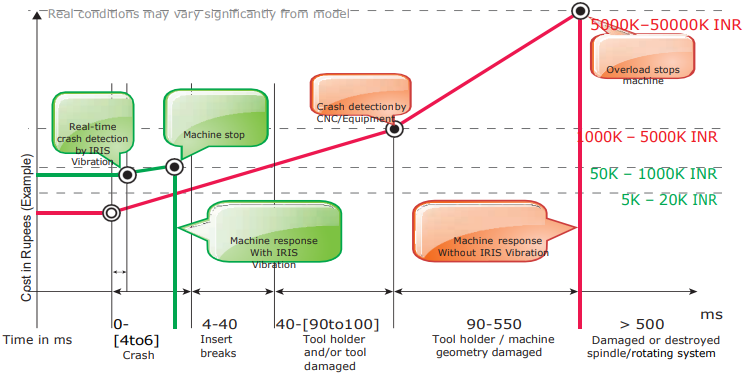
iVi is a device mounted on the spindle that gives real-time processed vibration data, real-time machine status, real-time processed vibration data, and more which reduces downtime and material costs with improved reliability.
iVi system architecture
- High speed DAQ board with multi sensor connectivity
- Real-time visualization on IRIS device
- Alarm logs transferred to IRIS Digital platform
IRIS iVi applications
m2nxt IRIS is designed and developed from a single integrated solution with a secure, robust and cloud based infrastructure. IRIS offers real-time monitoring, performance optimization, reporting and more to the future-connected factories. Here are the various applications of IRIS iVi:
CNC Machines
- Spindle mounted iVi Sensor to monitor collision
- Stoppage of the axes within 35~40ms of detection.
- Scenario based configuration enables caution to the operator/supervisor
Robotic Applications
- iVi Sensor mounted on the EOAT of the Robot – J6 axis
- Robot to stop mode with the sensor signal
- Scenario Teach Programming enables Operator of breach of normal vibration patterns
Gantry Systems
- iVi sensor mounted on the EOAT gripper of the Ram
- Servo Gantry can instantaneously stop upon detection of abnormal vibration and or Collision
- Scenario programming can be used to warn operator of breach of normal vibration patterns
IRIS components
- IRIS Edge Platform: An in-house built hardware for Industry 4.0 applications that can connect with any machines, collect data, analyze and visualize necessary parameters in near real time. It can be directly interfaced with controllers through Ethernet/OPCUA protocols or can be interfaced with external IO’s using Modbus.
- IRIS Digital Platform: Application with secure and robust infrastructure offered for monitoring near real-time data, machine health, productivity, maintenance alerts, overall equipment efficiency, plan vs actual productivity analysis, power consumption and many more.
How iVi benefits manufacturing companies
- To facilitate the adoption of cutting-edge technology for SMEs with cost-efficient solutions
- Recognized a market need, gap, and demand for machine monitoring and safeguarding solutions
- To alleviate operator concerns and minimize stakeholder risks
- To lower machine maintenance costs
- Offer user-friendly DIY installation mechanism with a self-explanatory installation manual that enables anyone to set up the system without expert assistance
Summing up
At m2nxt, we highly prioritize safety on all fronts. Alongside, we also give importance to applying innovative solutions to industrial manufacturing challenges, and maximizing productivity and performance on the shop floor. The implementation of iVi, a smart collision detection system, has enabled us to leverage our expertise to ensure safe shop floor environments across industrial manufacturing industries. If you’d like to explore iVi systems for your shop floor, reach out to our team to know more.